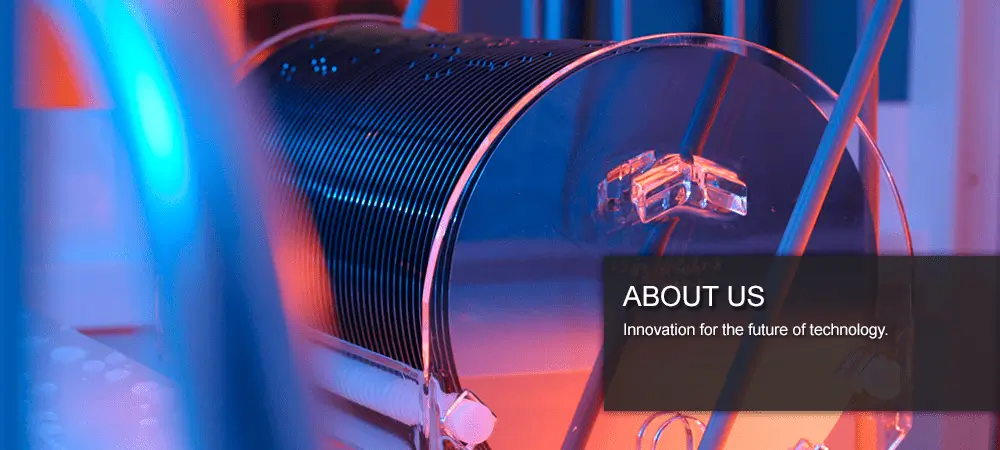
WHY CHOOSE GLOBALWAFERS?
We are a global leader in semiconductor technology, providing innovative, advanced technology solutions to leading chip manufacturers focused on transforming the foundation of a connected world. With R&D and manufacturing facilities in the U.S., Europe, and Asia, we focus on innovation throughout our business. As a trusted partner, we serve 100% of the top 25 customers in the semiconductor industry.